Corrosion under insulation (CUI) is one of the most well-known phenomena in the process industry and is also a big challenge for asset integrity management. If left undetected, CUI can lead to leaks and the shutdown of a process unit or an entire facility. Innospection performs the CUI inspection of topside and subsea assets with the next generation Pulsed Eddy Current Testing (PECT) technique.
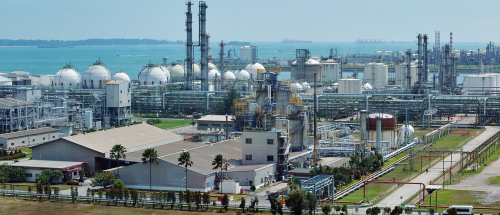
Corrosion Under Insulation (CUI)
PECT CAPABILITIES
Pulsed Eddy Current Testing (PECT) is a static non-destructive testing technique that measures the average remaining wall thickness of a defined inspection area (footprint).
The variation in the wall thickness is measured by the static time between the induced and returning field lines and is compared against a calibration.
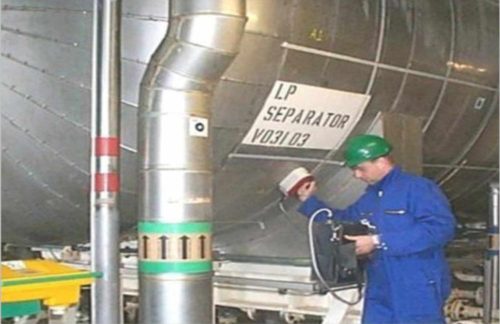
The capabilities of the latest generation include the ability to inspect through 250mm coating to measure the steel thickness beneath for corrosion hidden under the insulation and the ability to inspect through non-ferromagnetic and non-conductive insulation coatings and claddings.
- Concrete.
- Reinforcement bars in concrete coating.
- Aluminium and stainless steel sheeting.
- Plastic.
- Composite repair materials.
- Corrosion products like iron oxides.
Benefits
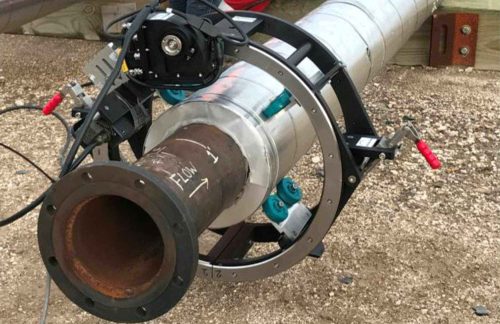
Inspection with the latest generation Pulsed Eddy Current Testing (PECT) technique offers notable advantages. It enhances wall loss detection capability and significantly increases operational speed. PECT’s highly repeatable readings make it particularly well-suited for monitoring the wall thickness of coated assets.
- Topside insulated pipes and pressure vessels.
- Insulated storage tanks and spherical tank legs.
- Concrete-coated subsea pipelines.
- Reinforced concrete-coated subsea pipelines.
- Coated risers, caissons and conductors.
Equipment
Powered by a dedicated battery located inside the data acquisition unit and two separate batteries for the tablet computer, the PECT equipment is powerful, fast and reliable.
A semi-automatic scanning ring has been developed to improve the inspection performance, particularly the timing and reproducibility. The electric motor of the scanning ring enables the circumferential step movements to be fully and remotely controlled by the operator.
The scanning ring is designed for adaptation to different topside pipe sizes and can also easily be deployed by rope access personnel. This offers a good solution for reducing scaffolding and rope access requirements during the inspection of suspended or elevated pipes.
Colour-coded wall thickness readings are displayed on the tablet computer during data recording. A file report can be generated quickly while the PC-based software is used for further analysis and reporting.
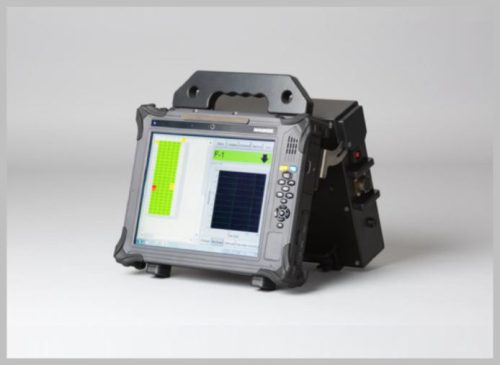
The PECT equipment consists of a ruggedised, splash water tight tablet computer connected to a data acquisition unit with four probe types able to accommodate a range of coating thickness up to 250mm.
- P1 (from 0mm to 20mm)
- P2 (from 20mm to 50mm)
- P3 (from 50mm to 125mm)
- P3 Subsea Probe
- P4 (from 125mm to 250mm)