Subsea structure inspection is performed on assets such as platform legs and sub-structures to identify defects and to evaluate the condition. Besides providing the inspection service, Innospection is also experienced in providing customised solutions to solve niche inspection challenges related to the subsea structures.
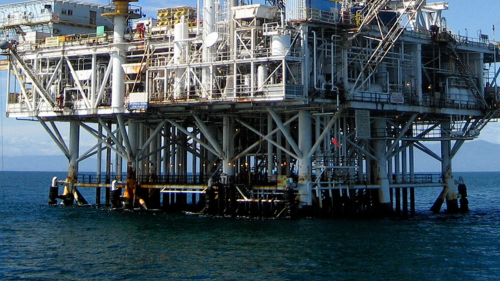
Subsea Structures
Capabilities
An expert in Eddy Current techniques for non-destructive testing, Innospection has extensive experience surface breaking crack detection on onshore assets such as pressure vessels, tank floors, duplex pipes and CRA liners as well as on offshore assets such as platform legs and sub-structures.
Such inspections are performed utilising various NDE techniques such as Eddy Current for external cracks, Time of Flight Diffraction (TOFD) for internal cracks, Ultrasonic for thickness mapping and/or laser triangulation system for geometry scan. The techniques are deployed by a scan frame customised to the project requirements and scan areas.
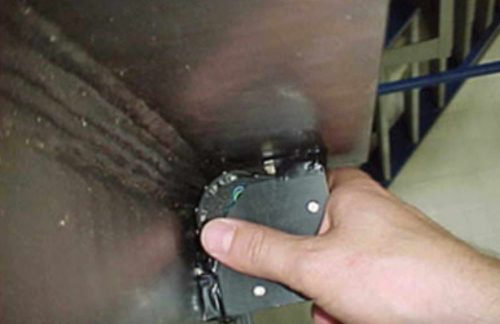
- Detection of fatigue-induced surface breaking cracks and leaks on welds and cast nodes of the platform legs and sub-structures, particularly at the critical areas with the highest stress level, utilising Eddy Current techniques.
- Inspection of platform structural legs for corrosion detection utilising next generation MEC (Magnetic Eddy Current) technique. A simultaneous marine growth cleaning and inspection operation can also be performed with the incorporation of an advanced cleaning system..
- Special cases such as the inspection of platform structural legs damaged by ship impact or platform legs with an unusual structure that obstructs the normal deployment of the inspection tool from the top..
Crack Detection with Eddy Current Technique
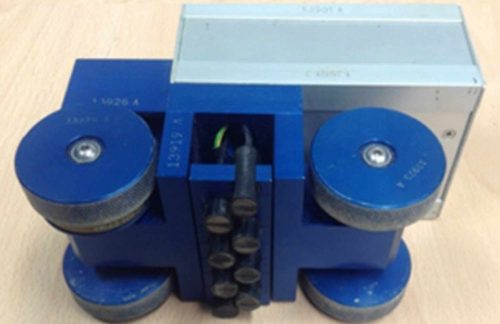
Eddy Current is known to be the most sensitive technique for the detection of surface breaking cracks as well as Stress Corrosion Cracking (SSC).
- The most suited technique for crack detection, with a detection probability of over 90% including through the coatings.
- It enables scratches to be distinguished from cracks when scanning in line with the feature (crack) orientation. The detection of cracks within an area of scratches is achieved by analysing the signal phase to signal amplitude and the variation of the Eddy Current frequencies used.
- Unlimited possibilities of arranging the Eddy Current sensors for adaptation to project scan requirements, detection scope and asset geometry. The crack detection sensitivity is the largest when the scanning is performed perpendicular to the orientation of crack.
Eddy Current Crack Detection Systems
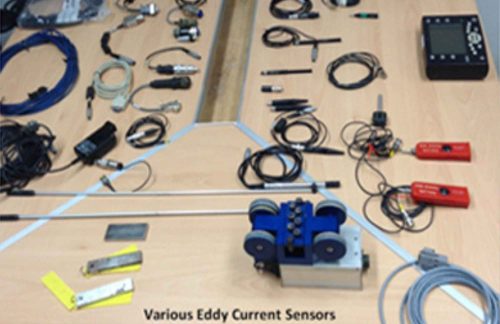
- Single Eddy Current sensor to be deployed by divers.
- Sensor array with multiple high resolution, spring-loaded Eddy Current sensors mounted onto a MEC™-Combi Crawler.
- Customised scan frames or manipulators incorporated with high resolution Eddy Current sensor array and encoded drive system optimised for the inspection tasks .
Corrosion Detection with MEC™ Technique
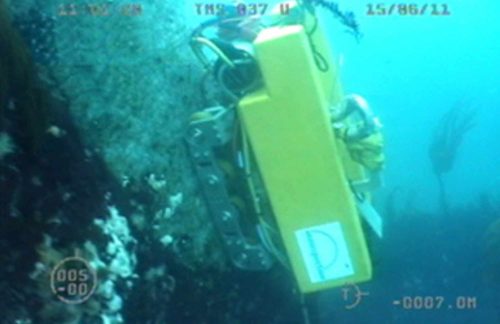
- High sensitivity and reliability in detecting internal and external defects including small and shallow pitting caused by bacterial corrosion (from Ø >3mm and 10% wall loss).
- No coating removal for a faster and more economical inspection operation.
- Analysis of defect severity in terms of volume and wall loss.
- Direct sizing of defects during scanning without the need for Ultrasonic verification with accuracy of +/- 10% for onsite reporting and +/- 5% for special offline analysis.
- Cleaning of the asset down to its bare metal to produce good quality data is not necessary which is a major advantage over Ultrasonic capabilities.
MEC™-Combi Crawlers
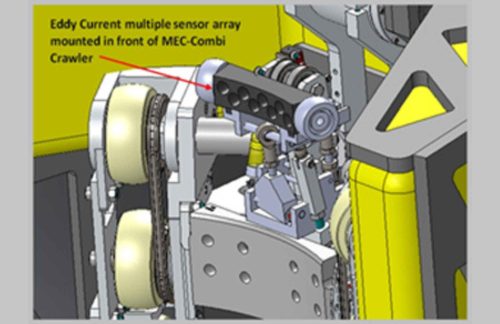
The sophisticated MEC-Combi Crawlers are designed and built to support subsea integrity assurance as well as to target inspection, deployment and subsea accessibility challenges.
- Cost effective inspection solution.
- Comprehensive inspection data within a single deployment through the incorporation of supporting inspection techniques such as: High resolution ultrasonic mapping, Pulsed Eddy Current Testing (PECT), Time of Flight Diffraction (TOFD), Laser triangulation system and Camera system.
- Deployable by diver or ROV from support vessels.
- Capable of self-crawling along the inspection surface to perform the scanning in axial and/or circuferential orientation.
- Ability to remain in stable contact with the inspection surface despite the turbulences and waves due to its integral buoyancy and magnetic system.